Across industrial sectors, sustainability is often framed around product outcomes—how a system performs in the field, how long it lasts, and how it reduces emissions over time. These are critical benchmarks, but they only reveal part of the picture. What happens upstream, in the steps that shape a product before it’s ever used, often goes unseen. Yet this is where many of the most meaningful shifts take place. In manufacturing, sustainability depends not only on how a product performs when in use but also on the choices made during production.
At Rochester Cable, we’ve been thinking more deliberately about that upstream view. And we’re seeing a clear shift across the industries we serve: supply chain resilience, material efficiency and operational transparency are no longer secondary considerations. They’re increasingly part of how organizations measure success.
As Earth Month brings renewed focus to the broader environmental conversation, we’re reflecting on the essential work of rethinking our systems from within.
Rethinking Waste: The Role of Scrap in Manufacturing

Material waste may not always be visible, but it’s persistent. In a high-output environment, even small inefficiencies can multiply quickly—adding up to more scrap, downtime and cost. Left unaddressed, it becomes an accepted loss. And in most cases, avoidable loss is the costliest kind.
There’s no singular solution to scrap. It shows up in different ways: miscalculations, changeovers, and offcuts too short to reuse. Picture a spool cut two inches short of specifications, or a length of cable that’s built perfectly but falls just outside usable dimensions. These items aren’t defective; they’re simply unusable.
Moments like these often go unnoticed in the flow of production, but they tell us something. They reveal opportunities to design smarter, build more efficiently and reduce the silent waste that chips away at performance.
Over the past several months, we’ve begun a more focused internal effort to understand and reduce scrap in our operations. This process is still taking shape, but it shares a common thread: increased attention to how materials are used, where losses occur and what it might take to close the gap.
Why It Matters to the People We Serve
Environmental impact isn’t only a concern for manufacturers. It’s also moving up the list of priorities for our customers—especially those in sectors like defense, energy and ocean technology. Project requirements are evolving. So are expectations.
The organizations we support are being asked to look more closely at the sourcing, durability and lifecycle cost of the materials they use. And increasingly, they’re extending those questions to their partners. It’s no longer just about meeting performance specifications—customers want to understand how products are made, how materials are handled and whether their suppliers’ practices align with their own sustainability goals.
For us, the ability to answer those questions with clarity is part of what defines quality. Being a U.S.-based manufacturer allows us to maintain that visibility and take responsibility for the impact of our operations—before, during and after production.
While customers may not always ask about scrap rates or process refinements, they often feel the results. Tighter systems lead to more consistent outputs. Less waste means more predictability. These outcomes matter just as much as product performance in the field.
A Culture of Efficiency and Accountability
Behind every cable we build is a system of decisions—about raw material use, production tolerances and how we respond when things don’t go as planned. Sustainability, in our experience, grows out of that system.
The mindset behind sustainability is what drives the small, intentional changes we’re making on the floor.
Whether it’s in how we forecast materials, train new employees or manage offcuts, the goal is the same: build well, waste less and hold ourselves to the kind of accountability we expect from others.
Progress, for us, means tightening what’s already in place and building from there.
Looking Ahead
Sustainability in manufacturing doesn’t begin with a sweeping overhaul. More often, it starts with a question: Could we do this better?
That question shows up in small moments—on the line, in planning meetings, during shifts where material use or process flow is reconsidered. And the answers don’t always come all at once. But they do build on each other.
At Rochester Cable, we’re focused on steady progress that turns intention into measurable change, and small improvements into long-term impact.
As the demands on our industry continue to evolve, so will our approach—not only to what we build, but how we build it.
Taking the Conversation Further at OTC 2025.png?width=773&height=435&name=Landing%20page%20image%20(Twitter%20Post).png)
We’ll be at OTC 2025 in Houston, TX, this May, where our team will discuss product performance, material use, and long-term reliability in the harshest environments.
Interested in how sustainability shapes our work on the ground?
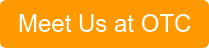